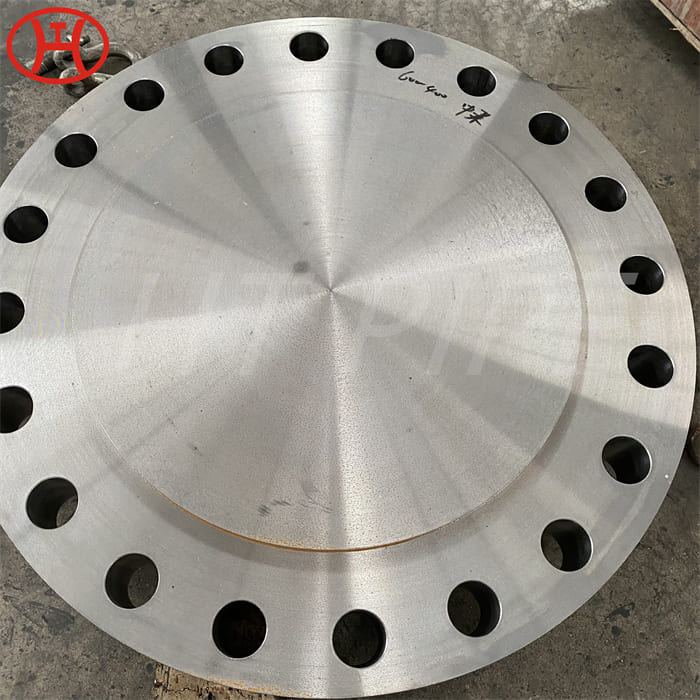
Alloy 31 Blind Flange ASME B16.5 Class 150 Flange
Alloy 31 is one kind of azotic contenting iron nichrome molybdenum alloy, the performance is situated between the super austenite stainless steel and the nickel base alloy, The presence of copper increases its resistance to sulfuric acid.
High Chromium Alloy 31 UNS N08031 Flange, W.Nr.1.4562 Blind Flange, ASME B16.5 Class 150 Flange
Alloy 31 Flange is used in the chemical and petrochemical processing industry . Alloy 31 Flange is also designated as UNS N08031 or DIN W.Nr. 1.4562, UNS N08031 Flange is an iron-nickel-chromium-molybdenum alloy with nitrogen and copper additions which has hybridized properties of austenitic super stainless steels and regular nickel alloys. W.Nr.1.4562 Blind Flange has exceptional corrosion resistance to alkaline & halide-containing media, sulfuric acid, phosphoric acid, chlorine dioxide media, nitric acid as well as reducing & oxidizing medias. ASME B16.5 Class 150 Flange is widely used in offshore & marine industries, chemical & petrochemical processing, pharmaceutical piping, oil and gas extraction, and ore digestion plants. Especially, Alloy 31 can be used for the fabrication of pressure vessels which may endure a wide temperature-range from cryogenic level to elevated temperatures(-196°C to 550 °C).
As advanced super-austenitic, high-chromium 6 M0 alloy called alloy 31 (UNS N08031) bridges the cost / performance gap between high-performance N i-Cr-Mo alloys and the 300 series stainless steels. High Chromium Alloy 31 Flange is especially suitable as a material of construction for the modern chemical process and petrochemical industries, where W.Nr.1.4562 Flanges must not only resist uniform corrosion caused by a range of corrodents, but also must have effective resistance to localized corrosion and stress corrosion cracking in halide and other media. Engineers have long known that chromium and molybdeniun improve resistance to localized corrosion. Alloy 31 UNS N08031 Flanges also have long known that increased amounts of nickel and nitrogen enhance resistance to chloride stress corrosion cracking. This knowledge led to a class of alloys that were very cost effective and provided corrosion resistance that in many cases approached or equaled the corrosion resistance of more expensive high Ni-Cr-Mo alloys in many environments. Cronifer 1925hMo (UNS N 08926) was derived from the 904L alloy and Nicrofer 3127hMo (UNS N 08031) was derived from alloy 28 metallurgy, by increasing the molybdenum content to 6.5% and fortifying the composition with 0.2% nitrogen.
- Chemical Composition Requirements
The Chemical Composition of Alloy 31, % | |
Nickel | 30.0-32.0 |
Chromium | 26.0-28.0 |
Iron | Balance |
Sulfur | ≤0.010 |
Si | ≤0.30 |
Manganese | ≤2.00 |
Phosphorus | ≤0.020 |
molybdenum | 6.0-7.0 |
Copper | 1.0-1.4 |
Nitrogen | 0.15-0.25 |
Carbon | ≤0.015 |
- Physical Properties of Alloy 31
Density | Melting Range | Permeability | Electrical Resistivity | ||
g/cm3 | lb/in3 | °C | °F | 20°C | µΩ·m |
8.05 | 0.290 | 1330-1370 | 2426-2498 | 1.001 | 104 |